Automated X Ray Inspection
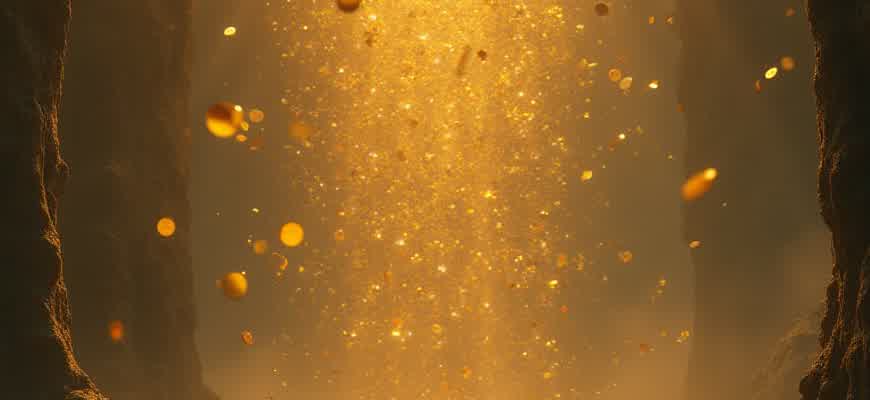
The integration of automated X-ray inspection technologies has revolutionized several industries, including the rapidly evolving cryptocurrency sector. This advanced method utilizes machine learning algorithms and high-resolution imaging to analyze and verify hardware components, ensuring their compliance with security standards. With cryptocurrencies becoming a cornerstone of digital transactions, ensuring the integrity of related hardware, such as mining rigs and wallets, is paramount. Automated X-ray inspection offers a non-invasive approach to detecting anomalies and potential risks in electronic devices used for cryptocurrency operations.
Key benefits of automated X-ray inspection for cryptocurrency hardware:
- Enhanced security: Detects counterfeit components or tampered devices.
- Improved accuracy: Identifies internal defects that could compromise hardware performance.
- Non-invasive process: Prevents any physical damage to critical components.
Common applications in cryptocurrency hardware:
- Mining hardware analysis
- Wallet hardware verification
- Device authenticity testing
"Automated X-ray inspection not only improves hardware security but also plays a crucial role in maintaining trust within the cryptocurrency ecosystem."
One significant aspect of using X-ray inspection is its ability to provide clear visual feedback through detailed imaging, allowing for precise identification of hidden issues in intricate circuit designs. This is especially important as cryptocurrency hardware becomes more sophisticated and complex.
Device Type | Common Inspection Issues |
---|---|
Mining Rigs | Overheating, wiring malfunctions, counterfeit parts |
Hardware Wallets | Corrosion, circuit defects, unauthorized tampering |
Reducing Human Error with Automated X-Ray Systems in Cryptocurrency Industry
In the cryptocurrency industry, ensuring the integrity of transactions and protecting sensitive data are paramount. One of the key challenges is preventing errors during security checks, especially when dealing with hardware wallets or physical transaction cards. Automated X-ray inspection systems are becoming essential in mitigating the risk of human oversight, providing consistent and accurate detection capabilities. By utilizing AI-powered image analysis, these systems can instantly identify potential issues, such as tampering or malfunctions in hardware components, that might otherwise be overlooked during manual inspections.
The automation of X-ray inspection significantly reduces human error, which is often a factor in delays or misidentifications during the verification of critical crypto assets. Automation in this area allows for faster and more reliable evaluations, making it easier to maintain high security standards and minimize potential losses. Furthermore, automated systems are designed to handle large volumes of items, ensuring that no asset is overlooked, regardless of the scale of operation.
Key Benefits of Automated X-Ray Systems in Crypto Security
- Accuracy: Automated systems use advanced algorithms to detect even the smallest anomalies, which can easily be missed by the human eye.
- Speed: Machines operate much faster than humans, enabling quicker turnaround times for security checks without compromising quality.
- Consistency: Unlike human operators, automated systems perform the same task with identical precision each time, ensuring consistent results.
- Scalability: Automated X-ray systems can process large volumes of data, ensuring seamless operation even in high-demand environments.
“Automated systems are designed to provide higher reliability and accuracy compared to manual inspection, particularly in the fast-paced and sensitive world of cryptocurrency.”
Comparative Analysis: Manual vs Automated X-Ray Systems
Factor | Manual Inspection | Automated X-Ray Inspection |
---|---|---|
Speed | Slower, depends on human performance | Much faster, consistent throughput |
Accuracy | Prone to human error, especially under stress | Highly accurate, AI-based image analysis |
Scalability | Limited by human capacity | Can scale to handle large volumes |
Cost Efficiency | Higher long-term costs due to training and human resource needs | Lower long-term costs after initial investment |
Key Benefits of Implementing Automated X-Ray for Industrial Applications
Automated X-ray inspection systems are revolutionizing industrial sectors by offering a more precise and efficient method for quality control. These technologies enhance the speed and reliability of detecting material inconsistencies, defects, or foreign objects in production lines. The ability to automate this process significantly reduces the chances of human error, making production more cost-effective and secure.
In the context of industrial applications, these X-ray solutions are particularly effective for inspecting products in the automotive, electronics, and food industries. The speed and accuracy of the system allow manufacturers to quickly identify potential issues, reducing downtime and improving overall efficiency in production cycles.
Advantages of Automated X-Ray Inspection
- Increased Accuracy: Automated systems ensure consistent, high-resolution imaging that human operators may miss, providing more reliable results.
- Higher Throughput: Automation significantly speeds up the inspection process, allowing for faster production times and reducing bottlenecks in the manufacturing process.
- Cost Efficiency: By reducing the need for manual inspection, companies can lower labor costs and prevent costly errors related to faulty products.
- Real-time Feedback: Automated systems offer immediate detection and analysis, enabling quick responses to production issues and reducing delays.
Automated X-ray inspection offers a faster, more accurate alternative to traditional methods, making it a key component of modern industrial quality control systems.
Key Impact Areas
- Product Quality: Continuous monitoring helps ensure that only defect-free products make it to market, improving brand reputation and customer satisfaction.
- Safety: Automated systems can detect potentially hazardous foreign objects in products, which is especially crucial in sectors like food and pharmaceuticals.
- Regulatory Compliance: Automated systems help ensure adherence to industry standards and regulations by providing detailed inspection records and data analytics.
Comparison of Traditional vs. Automated X-Ray Inspection
Aspect | Traditional Inspection | Automated X-Ray Inspection |
---|---|---|
Inspection Speed | Slow, manual process | Fast, real-time analysis |
Accuracy | Prone to human error | High accuracy with minimal error |
Labor Costs | High due to manual involvement | Reduced, as most tasks are automated |
Integrating Automated X-Ray Systems into Crypto Mining Production Lines
Integrating automated X-ray inspection systems into cryptocurrency mining operations can significantly enhance quality control and component validation. With the growing complexity of mining hardware, ensuring the integrity of the internal components is crucial for maintaining operational efficiency and minimizing downtime. These X-ray systems provide a non-invasive way to detect flaws in circuit boards, chips, and connectors, which is essential for reliable mining performance.
To successfully integrate such systems, the process must be carefully planned and aligned with the existing production flow. Key factors such as equipment compatibility, space requirements, and throughput must be taken into account to prevent disruptions. The following steps outline a structured approach to achieving seamless integration in a crypto mining production line.
Steps to Integrate Automated X-Ray Systems
- Assess Current Production Line: Identify areas where inspection could enhance product quality, such as PCB assembly or chip mounting.
- Evaluate X-ray System Compatibility: Choose systems that align with the size, resolution, and speed requirements of your components.
- Install the X-ray Unit: Ensure proper placement for optimal scan coverage without interrupting the existing flow of the production line.
- Integrate Software Solutions: Ensure seamless data exchange between the X-ray system and the production monitoring software for real-time quality feedback.
- Training and Calibration: Provide operator training and calibrate the system to account for component variations and optimal imaging settings.
Key Considerations for Successful Integration
Factor | Details |
---|---|
System Speed | Ensure the X-ray inspection speed matches the throughput of the production line. |
Quality Standards | Define clear inspection criteria to ensure uniformity in results. |
Maintenance | Regular calibration and maintenance schedules should be established to maintain performance. |
"Automated X-ray inspection not only boosts quality assurance but also helps identify potential issues early, reducing costly downtime and improving overall mining hardware performance."